Composite film adhesive layer does not dry phenomenon loss,Here's the trick
After the composite product has been cured at a certain temperature and time, the interlayer peeling composite film adhesive layer still has a certain viscosity, that is, after the composite film peeling, the two-layer film will be re-glued together by hand, and the severe drying of the composite film adhesive layer will directly affect the peeling strength of the composite film, while the slight non drying phenomenon will lead to poor heat sealing strength after bagging, and the viscosity after the interlayer peeling. Heat sealing place is easy to wrinkle phenomenon, but storage a week or half a month later, packaging bag wrinkle phenomenon, this phenomenon, caused by the loss is often larger.
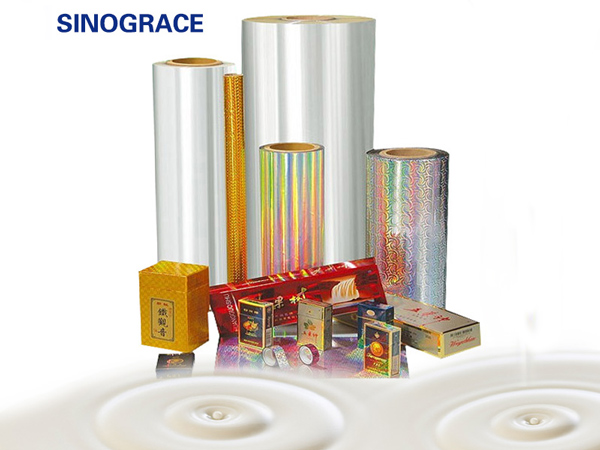
Causes of non -drying composite film
1.The ratio provided by the glue manufacturer is not accurate, the proportion of curing agent is too small or the ratio of mixing glue liquid is misadjusted, and the curing agent is too little or ineffective.
2.In addition to dilute the solvent water or small molecular alcohol content is too high consumption of curing agent
3.Film moisture absorption, especially NY and cellophane, it is easy to appear not dry phenomenon.
4.The use of ink containing alcohol solvent does not volatilize completely resulting in the glue layer is not dry.
5.The use of polyurethane, polyester ink without hardening agent caused by the glue layer is not dry phenomenon.
6.The ambient temperature and humidity are too high, the prepared adhesive is placed for too long, resulting in the curing agent and water reaction for a long time.
7.Containing K coating PET film composite machine PET film additive influence.
Corresponding solution
1.Generally speaking, the ratio provided by adhesive manufacturers is a reasonable ratio obtained through a large number of tests by adhesive manufacturers. Therefore, the ratio will not be inaccurate. If indeed because of the quality of the adhesive itself must be replaced by the adhesive;
2.Reduce the total content of water and alcohol in ethyl acetate (replace good quality ethyl acetate, the total content of water and alcohol is less than 0.2%);
3.When the composite moisture absorption NY and cellophane film adjust to improve the proportion of curing agent (5% ~ 10%), at the same time do not use damp film;
4.As far as possible to reduce the amount of residual solvent in printing ink;
5.The use of polyurethane ink: the first is to solve the composition of polyurethane ink dilution solvent, try to do not use alcohol dilution solvent. If alcohol diluent must be used when printing, it should also be done in printing to minimize the residual solvent;
Secondly, if there is a printing film with white ink, finally, a small amount of hardener is added to white ink, which can increase the compound fastness. But added hardener ink use period is shorter, if there is surplus, and the interval time is longer in principle should not be used again. Finally, the purity of ethyl acetate used for preparing adhesive dilution should be high, and the content of water and alcohol should be as low as possible, which is the quality assurance of cooking bag and dry compound. In addition, when preparing adhesive, the dosage of curing agent should be increased appropriately (the increase proportion is between 5% and 10% of the curing dose, That is to say, adding 1 kg of curing agent needs to add 0.05-0.5 kg of curing agent) to ensure that the main agent of the adhesive and curing agent fully crosslinking.
6.The compound environment must be controlled, such as placing exhaust fans indoors to strengthen indoor air circulation, but be careful not to blow against the compound machine. When compound, always pay attention to the scraper and guide roller near the rubber groove, there is no water beads, and reduce the speed at the same time, because the speed is too fast, the local temperature near the rubber groove is too low, should cause water vapor condensation;
7.Shorten the storage time of prepared adhesives. When preparing adhesives, reduce the amount of preparation each time, increase the number of preparation times, shorten the storage time, improve the drying temperature and reduce the amount of residual solvent. This reduces the effect of water and alcohol on the hardener, allowing as much water and alcohol as possible to evaporate in the drying channel.
At present, our company's waterborne adhesive and and waterborne Lamination Adhesive, has been put on the market, the market feedback is good, the performance is excellent, fully able to meet the complex needs of customers of various packaging structures.
